3. Structural analysis of the product
Due to the complex structure of the product, we constructed a structural analysis of the above model based on the ANSYS software platform. With the development of computers and computing methods, complex engineering problems can be solved by discretized numerical computing techniques and computers. Numerical simulation technology is one of the important impetus for the formation and development of modern engineering. At present, the most widely used numerical simulation method in engineering field is finite element method. The finite element calculation result has become a reliable basis and effective means for design and performance analysis of various industrial products. ANSYS software is a large-scale general finite element software integrating structure, heat transfer, fluid, electromagnetic, acoustic and blasting analysis. Its developer ANSYS is one of the world's most famous companies in the CAE industry, and has been designing and analyzing for a long time. Software development and development. Many international companies use ANSYS software as the standard for their design analysis. With a wide range of users around the world, ANSYS software has become one of the most effective software in the field of computer-aided engineering and engineering numerical simulation.
First, we import the 3D solid model built in the Pro/engine environment into the ANSYS software environment, and then establish the boundary conditions for calculation. In the residual deformation test, due to the slight plastic deformation of the product, we based on the VON MISES yield criterion in plastic theory.

That is, we use nonlinear elastoplastic static structure analysis. The analysis steps are as follows: Establish geometric models, define material properties, unit related properties, mesh, apply constraints and loads, and finally solve. Through the analysis of the above steps, the following VON MISES equivalent stress cloud map is obtained (see Fig. 8, Fig. 9, Fig. 10 and Fig. 11). Compared with the VON MISES equivalent stress cloud results, the maximum stress distribution area of ​​CLIP-3 is small, and the maximum stress distribution area of ​​CLIP-3-1 is large.
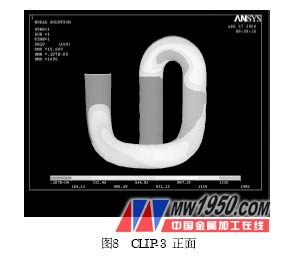
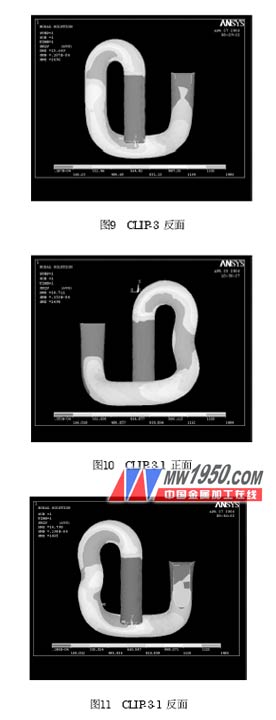
The maximum strain value of the CLIP-3 is 0. 002805mm, and the maximum strain value of the CLIP-3-1 is 0. 00347mm. The results of the VON MISES PLASTIC STRAIN cloud map (see Figure 12 and Figure 13) are compared. Through the above analysis, it is concluded that the plastic deformation of CLIP-3-1 is greater than that of CLIP-3, so that the permanent deformation value of the toe end of CLIP-3-1 is unqualified after the residual deformation test.
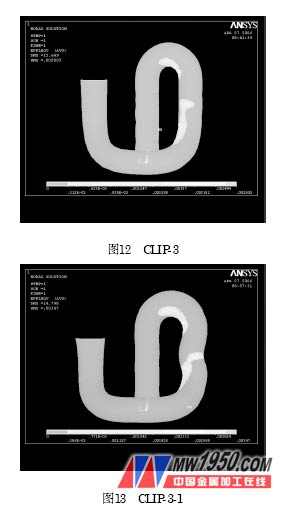
4. Comparison of residual deformation test
The permanent deformation values ​​of the toe end of the CLIP-3 and CLIP-3-1 residual deformation tests are shown in the table below.
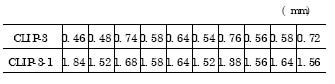
The data in the table can be seen: The permanent deformation value of the toe end of the CLIP- 3- 1 residual deformation test is greater than 1. 0mm, the product is unqualified. Lmm-3 The residual deformation of the toe end of the LIP-3 residual deformation test is less than 1. 0mm, the product is qualified.
5 Conclusion
In the production process of the elastic strip type III fastener, the product is bent laterally due to the production process problem, so that the maximum stress distribution area of ​​the elastic strip type III fastener spring strip becomes larger, and the maximum strain value becomes larger, thereby The permanent deformation value of the toe end of the elastic deformation test of the type III fastener was unacceptable. To this end, we have carried out the improvement of the production process, strictly control the shape of the heel end, ensure that it is laterally straight, does not produce lateral bending, and better solves the permanent deformation value of the toe end of the elastic deformation test of the type III fastener. The problem of unqualified quality guarantees the buckle performance and eliminates the hidden dangers of train driving.
Previous page