4. Statistics and analysis of the yield of lost foam casting
The yield statistics of lost foam casting are shown in Table 3.
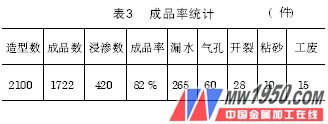
As can be seen from Table 3, water leakage is the main waste product in the production of lost foam casting. If this problem is solved, the yield of castings can reach more than 90%. The solution is as follows:
We first sampled the leaked parts and cleaned them with acetone. The surface elements were chemically analyzed by electron spectroscopy. Then, the samples of the leaked parts were fixed by polishing and nitric acid solution, and then microstructured by metallographic microscope. Observe, the results are shown in Figures 10-12.
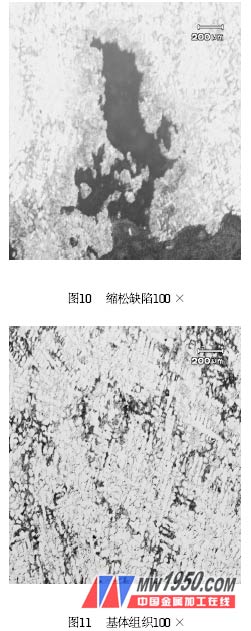
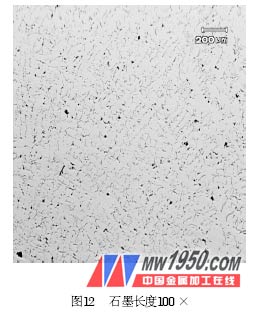
Elemental energy spectrum analysis showed that the content of carbon in the surface structure of the water leakage part of the casting was the most. It can be clearly seen from Figures 10 to 12 that there is a significant shrinkage defect in the surface structure of the water leakage part of the casting, the graphite form is a branched wafer shape (E type), the graphite length is 3 to 6 mm, and the matrix structure is about 85. %F+ P (sample size is 5mm × 4mm × 4mm, the main inspection instrument is inverted metallographic microscope, the test basis is GB 7216 - 1987). This suggests that during the lost foam casting production process, the casting of molten iron does not completely burn and decompose the foam model, but that residual carbide remains in the interior of the casting and along the cross section of the casting. Interconnecting each other constitutes a penetrating carbon inclusion. After the cylinder head is processed, the water pressure test is carried out, and under the pressure of 0. 4MPa for 2 minutes, leakage will occur. When the residual amount of such carbides is small, and the water leakage phenomenon is only a slight leakage, it is also possible to block the impregnation hydraulic pressure into the leakage portion by high pressure (about 0.7 MPa); There are many residual amounts of carbides, and the leakage phenomenon is serious. Castings can only be disposed of. In order to reduce the residual amount of such carbides in the casting, we have taken the following measures: reducing the pre-expansion density of the beads, the hollowing-out process of the sprue foam model, the integral foaming of the sprue and the sprue, and the use of the model cluster. The integral one-time dipping coating and the in-type negative pressure at the time of casting molding are remarkable, and the effect is remarkable.
As the production practice deepens, we find that the shrinkage defects shown in Figure 10 also appear in the castings formed in the loose parts of the foamed die.
This is mainly due to the unstable quality of the pre-formed beads, which causes the foamed mold sheets to be loosened during the molding process, and the coating material penetrates into the foamed mold during the dipping process, so that the cast castings have the defects of the coating paint, and water leakage occurs here. . To this end, we should adopt the method of appropriately increasing the pre-expansion temperature and shortening the curing cycle to minimize the volatilization of pentane to improve the degree of fusion between the beads inside the mold during molding; on the other hand, the test is electrically heated. The way to carry out the pre-expansion of the beads, and strive to minimize the amount of pentane volatilization. Both methods have received good results.
Fourth, the cost advantage of the engine cylinder cover lost mold cast iron parts and the test of the installed bench
1. The cost advantage of the engine cylinder cover lost mold iron parts
We use the N485 (DI) engine lost foam casting cylinder head (see Figure 13) as an example to compare with ordinary sand castings. As a result, the weight of the lost castings is reduced by 5kg (the lost mold casting weight is 39kg, and the ordinary sand casting weight is 44kg). . If the total production cost per unit price of lost foam casting is calculated, the total production cost of lost foam casting is 650 yuan per ton compared with ordinary sand casting. The total production cost of lost foam casting is about 5250 yuan per unit. The total production cost of sand casting is ton unit price is about 5900 yuan). For the mass production characteristics of the automotive industry, the use of the lost foam casting process to organize the production of engine blocks and cylinder heads is cost-effective and has significant economic benefits.
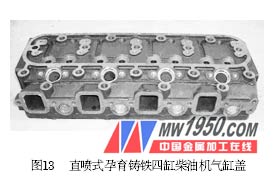
Previous Next